Call David at
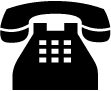 |
07817025625
(Daytime number) |
02085618483
|
|
Previous work carried out on behalf of the following:
Alfred Beck Theatre
Anne Liebeck (Soprano)
Chas ‘n’ Dave
David Gray
Des O’Connor
Elton John
Hampton Court Palace
Her Majesty’s Theatre (Phantom of the Opera)
Ian Drury
Jools Holland
Royal Ballet School, Richmond
Russ Abbot
Sid Lawrence Orchestra
Wycombe Swan Theatre |
|
Technical Stuff
Tuning Plank
Re-Stringing
Soundboard
Hammers
Key Bushings
Action
Regulating
Tuning Plank
The tuning plank or ‘Wrestplank’, [or ‘Pin Block’ if you are an American] is the name given to the hardwood plank that runs the entire length of your piano, into which the tuning pins are driven. It is usually made of Beech; on older instruments a solid plank is used with a thinner layer of Beech ‘capping’ glued to the front face, with the wood grain running in the opposite direction to the main plank. Tuning stability is dependent on how tight the tuning pins are in the Wrestplank, if the wood fibres fail to ‘grip’ the pins, they will slip and the instrument will go badly out of tune. This is a common problem when older pianos are in a centrally heated environment; the plank dries out, the old-fashioned animal glue holding the capping breaks down, and the plank splits between the pins along a grain line [old Bechstein model IV uprights often exhibit this problem in their Tenor range, where the pins are grouped very close together].
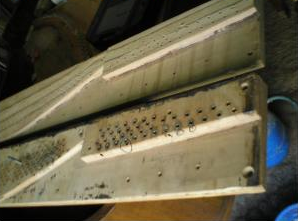 |
When a piano is re-strung, a slightly larger diameter tuning pin than its predecessor is driven into the plank, but if the plank already has a fracture, this will just exacerbate the problem as the crack opens further and ‘creeps’ to the next pin along the grain. The ONLY realistic remedy, is to replace the plank with a modern multi-laminated beech that cannot possibly split again. It is a procedure that is carried out in conjunction with re-stringing, and whilst it is an expensive, time consuming job, the end result will be an instrument that will hold its tune for a much longer period. |
On the above: Old plank and newly crafted laminated plank for a Schiedmayer Grand. Note the staining on the pin holes of the original plank where ‘pin tightening’ fluid has been previously applied in an attempt to solve the problem to no avail!
RE-STRINGING
Re-stringing is carried out on a piano for a number of reasons; either the instrument does not hold its tune well, as the tuning pins have become loose, or the wire is ‘tired’ and prone to breakage, Bass strings are ‘buzzing’ or have gone dull and ‘tubby’, or the ‘crown’ of the soundboard has deteriorated giving the instrument a weak tone. Provided the Wrestplank is sound, [see above] the piano can be re-strung using the next pin size up from the originals.
SOUNDBOARD

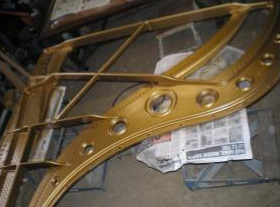
|
The soundboard is responsible for amplifying the sound of the strings via the bridge. If the soundboard is subjected to an excessively dry environment, there is a danger that it will develop splits, which can result in annoying buzzing sounds!
Any soundboard splits can be professionally repaired and the board re-finished in conjunction with a re-string, as the iron frame is taken out of the piano, allowing full access to the soundboard. The board is made of spruce, and any splits must be repaired using the same material….not filler!
Whilst the frame is out of the piano, David re-gilds it, [unless a customer wants it left in its original condition] – this is purely cosmetic, but does give a beautiful appearance to the inside of the piano, especially if it is a Grand, where the top is often raised. |
HAMMERS
The hammers are one of the main contributors to the character and tone of your piano. Over years of playing, they become flatted/pitted, and the tone alters as the felt on them becomes compressed. The hammer felt can be re-shaped and ‘voiced’ a couple of times, but eventually they will have to be re-covered or the heads replaced. David favours fitting a brand new set, an extremely skilled job, as the ‘strike’ line of the hammers is critical to an even tone. He uses West German Hammers made by Helmut Abel.
KEY BUSHINGS
After a number of years of use, the key bushings wear. There are two rows of bushings, one on the pivot/balance point, [chasing bushings] the other on the underside of the fronts of the keys. Worn chasing bushings affect the touch depth of the keys, often causing hammers to double strike [this is called ‘blubbering’] and the key to ‘lean’ over. Worn fronts result in the keys fouling on the adjacent key. Both problems should be rectified by replacement, before an instrument is regulated. Moths are also the bane of the felts under the keys, the felts, being made of wool fibre and seldom cleaned out, provide a food haven for moths and their larvae.
ACTION
Basically the ‘action’ is the mechanism of a piano enabling the hammers to strike the string via the depression of the key. There are at least four moving hinges, [centres] to each note, any one of which, if too tight, will affect the touch weight and responsiveness of a note. There are preparatory fluids sold to apply to the centres if this is the case, as a cheap fix. David prefers to replace the worn or corroded centre pins with new ones. Grand actions of the ‘roller’ type repetition action, have an extra lever that throws the hammer up slightly as soon as pressure is relaxed on the key, thus enabling the ‘jack’ to return under the roller to repeat the note at speed. It is important that the roller has not become flattened on its underside, otherwise the ‘jack’ will not be able to function without resistance.
Upright pianos do not have this feature, but attempt to increase repetition by having a spring at the base of the hammers, [the butt spring] attached to a loop on its pivotal flange. On uprights, the process is further aided by a leather ended tie tape, which helps to pull the hammer back to its return position. These tapes often rot and break on old pianos and are among the first items that need replacement with age, along with the butt springs, flange loops and often worn balance hammer leathers – a full action re-build is a time consuming business.
Damper felts also harden over time, and the springs, [on upright pianos] that propel them against the strings to stop the note after it has been played, also weaken, causing unwanted and lengthy sustain of notes. All of these items should be inspected and rectified if required, before the action is finally regulated for optimum playing satisfaction.
REGULATING
The term given to the adjustments of the piano to make it perform correctly. On both Grand and upright actions, a procedure has to be carried out in a specific order. Spacing of the hammers to the strings is generally the first task performed, followed by the setting of the strike distance [the Blow] of the hammer to the string. On a grand ‘Roller’ action, the jack must be in the correct position under the roller before the strike distance of the hammer is set. Then the jack escapement is set, followed by the distance from the strings that the hammer is held fast after the note is struck, referred to as ‘the check off distance’. Keys are leveled with various paper shims under their fulcrum point, [the balance] and must result in a touch depth of at least 10mm, [with the exception of the old Blüthner Grand patent action] otherwise there is not enough key travel for the action to perform properly. Lastly on the roller Grand action, repetition and the often forgotten hammer ‘drop’ is set by adjusting the little screw in the hammer flange ... so there you are, if we tell you all any more, you would all be able to ‘do it yourself’!!!
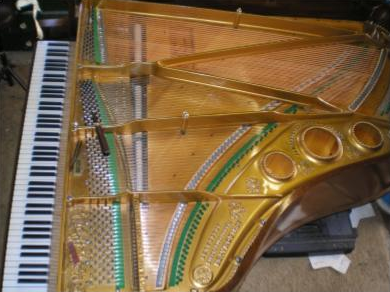
|